Revolutionizing Remote Handling Part 1 – How VR4Robots Enhances Robotic Engineering
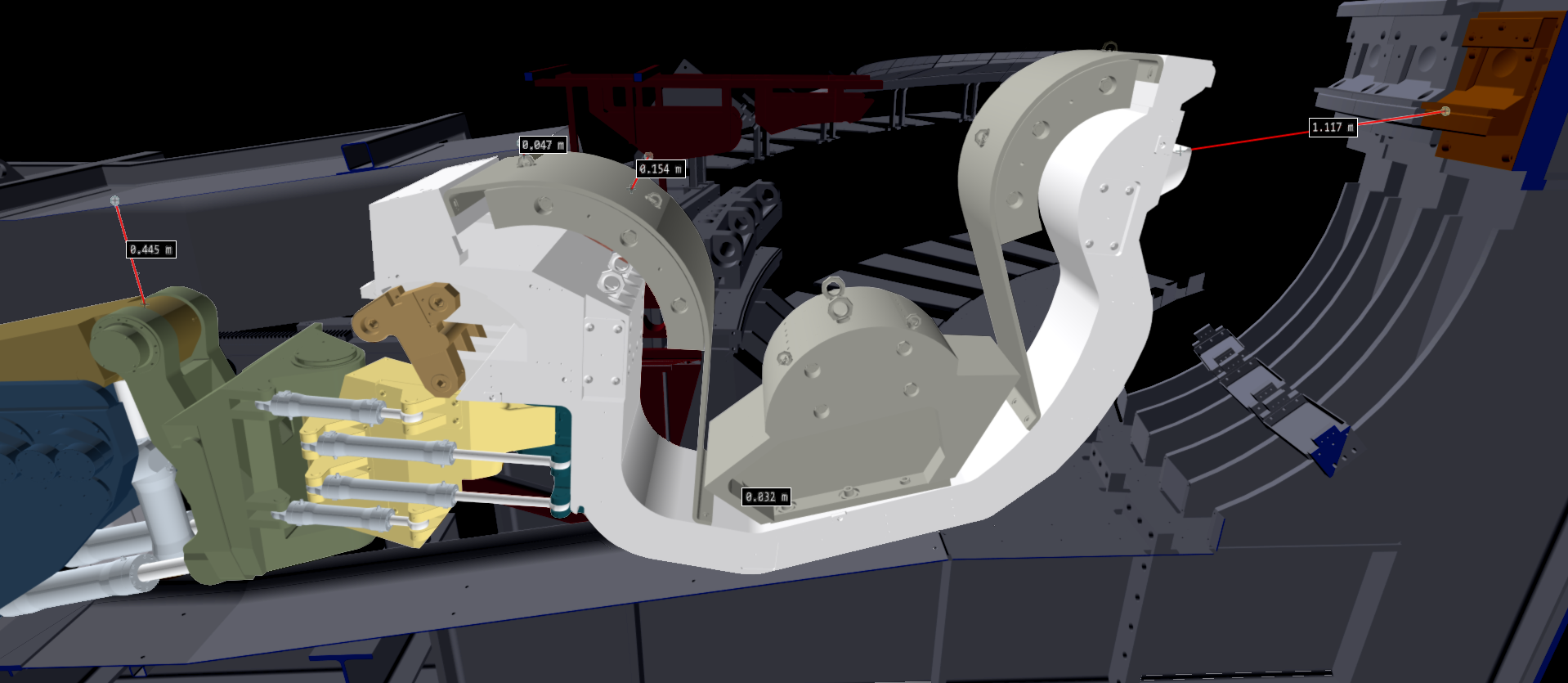
Image courtesy of Fusion For Energy
Companies involved with complex remote handling operations in high-risk environments – such as nuclear power plants – have a need for innovative and cost-effective solutions to optimize safety and efficiency. VR4Robots – Tree C’s powerful and robust robot simulator – is changing the way engineers and product owners approach the development of remote robotic systems.
In a new series of blogs, we’ll be exploring how VR4Robots can add value at each stage of highly complex and high-risk remote handling projects, from engineering to training and operations. In this first installment, we focus on the engineering phase – where crucial design decisions must be made.
The value of virtual robots in prototyping
When you’re designing remote handling equipment for complex operations, such as nuclear reactor decommissioning, there are many engineering hurdles to overcome – not least the cost of prototyping. Virtual robots can provide a cost-effective solution, usually in the form of standalone CAD models.
Digital CAD models might be an integral part of the modern design and engineering process, but approaches to prototyping have yet to fully embrace digital solutions. For that reason, when prototyping complex remote handling equipment, physical models, costly design iterations, and extended development timelines are still common.
Another drawback to these CAD models is that they’re developed in isolation, which impairs their ability to interact with end-effectors, the environment, and surroundings. As a design validation tool, this limits their usefulness. In other words, it’s not possible to use them to fully validate and test designs before physical prototyping begins.
Thankfully, it’s here that our real-time interactive visualization technology for remote handling, not only comes into play – but excels. With VR4Robots you get much more than a standalone digital model of your robot; you get a complete virtual world built on our powerful yet flexible simulator framework.
How VR4Robots improves remote handling operations
With real-time physics simulation, engineers can analyze how gravity, collisions, and mechanical forces impact a robot’s performance, long before you begin building a physical prototype. A fully interactive virtual environment lets you safely test robotic systems in realistic, real-world conditions. In fact, it helps create a valuable picture from which you can draw reliable conclusions that feed into your design.
Companies involved in areas such as nuclear decommissioning, reactor maintenance, and hazardous material handling rely on robotics for safety and efficiency. The cost of errors in these industries is high – not just financially but in terms of operational safety.
Without VR4Robots, companies often resort to building physical prototypes too soon, leading to expensive and time-consuming redesigns. At the same time, less sophisticated digital tools lack the physics simulation capabilities necessary for accurate predictions, resulting in misleading design conclusions or impossibilities that lead to operational failures.
The main features of VR4Robots for engineers
VR4Robots gives you an extensive range of capabilities designed to streamline and enhance the engineering phase, including:
- Real-time physics engine– Accurately replicate real-world physics, including center of gravity, inertia, collision responses, and material interactions.
- Full virtual environment representation – Simulate the entire worksite, integrating robots, tools, and surroundings for the complete validation experience.
- Advanced kinematics and dynamics modeling – Get precise control over robot movements, including joint flexibility, forces, and torque.
- Collision detection and response – Identify potential design flaws by simulating real-time interactions between robots, tools, and the operating environment.
- Load and stress analysis – Simulate weight distribution and structural integrity when lifting or manipulating heavy objects, including bending and drooping.
- 3D measurements and cross-sections – Measure spatial constraints and view obscured or cluttered environments with ease.
- Point cloud data integration – Import real-world laser scan data to accurately simulate existing environments for validation against actual conditions.
- Free camera navigation – Inspect designs from multiple perspectives using full 3D navigation.
The benefits of VR4Robots in robotic engineering
By integrating VR4Robots into your engineering workflow, you gain several powerful advantages:
💰 Reduced development costs
Building multiple physical prototypes is expensive. VR4Robots allows for extensive virtual testing, minimizing the need for physical mock-ups, and reducing costly redesigns.
🏃 Faster design iterations
With real-time simulations, you can quickly identify and resolve issues that would otherwise require physical testing, accelerating time-to-market.
🎯 Accurate and reliable equipment validation
Beyond CAD models, VR4Robots provides dynamic testing in a realistic operational environment, ensuring robots can perform effectively under real-world constraints.
🎛️ Test and refine operational sequences
Not only can you use VR4Robots to test robotic equipment, you can use it to evaluate operational sequences, making improvements where needed.
☢️ Increased safety and risk reduction
By simulating robotic operations in hazardous environments, engineers can predict failure points and operational risks before deployment, improving safety outcomes.
📡 Improved communication and collaboration
VR4Robots serves as an interactive visualization tool, making it easier for engineers, stakeholders, and clients to align on design decisions earlier in the engineering process.
A game-changer for engineering remote handling tools
With increasing investment in nuclear energy, including the rise of small modular reactors (SMRs) and fusion projects, the need for advanced robotic simulation is greater than ever.
VR4Robots is already playing a key role in projects such as the ITER fusion reactor in France and decommissioning efforts in Fukushima, Japan, proving its value in high-stakes environments.
By adopting VR4Robots early in your engineering process, you can achieve greater efficiency, cost savings, and operational reliability in your remote handling projects.
What’s next?
In our next blog on VR4Robots, we’ll explore how the VR4Robots model can transform operator training, ensuring a seamless transition from engineering to real-world application.
Interested in learning more about how VR4Robots can optimize your engineering workflow? Contact us today for a demo and see how simulation can revolutionize your approach to robotic engineering for remote handling operations.