Hardware-In-The-Loop Simulators For Marine Environments Explained
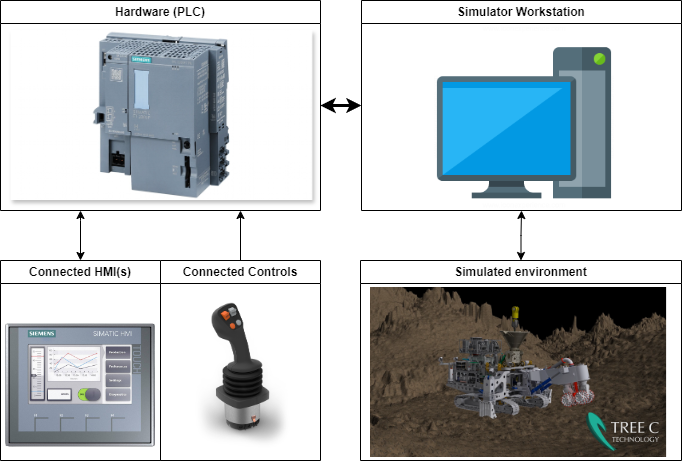
Hardware-in-the-loop is a type of simulator setup that has multiple benefits for complex operations in high-risk environments. You can use it to greatly enhance operator training, control system engineering, and your sales and marketing efforts.
As a training resource, HIL gives trainees hands-on experience of real-life operations with none of the risk. From an engineering perspective, it’s a cost-effective way to design, test, and validate control systems and equipment. On top of that, it’s a powerful sales tool for manufacturers to demonstrate equipment, and for companies to showcase their capabilities, using highly-realistic simulated equipment and environments.
In this article, we explore the use of HIL simulators to support companies working in and around complex offshore, subsea, and remote handling operations.
What is hardware-in-the-loop?
Hardware-in-the-loop (HIL) is a testing and simulation technique used in many fields of engineering. HIL integrates actual hardware components with a digital simulation of equipment and environments. A minimal HIL setup includes:
- a desktop PC
- a network connection
- a Programmable Logic Controller (PLC) from the real equipment
- the actual control console or Human Machine Interface (HMI) screens (optional)
In an HIL setup, the control system behaves as if it’s talking to the real system. HIL allows engineers to validate the performance of hardware and control systems in real-time under conditions that closely resemble their intended real-world use. For that reason, it’s an ideal solution for training operators on specific equipment and missions.
The beauty of this type of simulator is that it doesn’t lie; it makes visible what’s programmed in the PLC. It’s as close as you can get to the real thing without actually being there. For that reason, any features or anomalies in the real system will also be present in the HIL simulator.
The ability to connect physical hardware and embedded software with a digital environment that behaves like the real world gives companies involved with complex operations – such as Allseas – the ability to deliver sophisticated operator training programs.
Why use a HIL simulator for operator training?
Here are seven core benefits of using HIL simulators for operator training:
- Cost-effectiveness: Training with HIL reduces the need to commandeer the use of actual vessels and equipment (by temporarily taking them out of service), significantly cutting costs.
- Realistic training scenarios: HIL provides operators with hands-on experience in simulated environments that mimic real-world offshore and subsea conditions.
- Safe learning environment: Trainees can practice handling critical systems, also in off-normal situations or emergencies, without risking damage to equipment or endangering lives.
- Emergency preparedness: HIL allows trainees to experience and respond to simulated emergencies, such as blowout preventer (BOP) failures or dynamic positioning (DP) system malfunctions, improving readiness for high-stakes situations.
- Customizable scenarios: Operators can train for specific tasks, such as a critical lift or specific subsea installation.
- Practice remote handling: HIL enhances operators’ skills in controlling robotic arms, manipulators, and other remote-handling tools in complex subsea operations.
- Flexible learning: Engineers and operators can use HIL to stay up-to-date on new technologies and processes without requiring expensive on-site training sessions. The simulation software and the computer hardware needed to run it – can be easily packed into flight cases and shipped to different locations to train operators wherever they are stationed.
How can HIL simulation bring value to your operations?
From both engineering and business perspectives, HIL simulation delivers value across a number of different areas. Here are some of the key benefits:
- Early error detection: Connecting embedded software to the simulator environment makes it possible to surface flaws before they impact real-world operations.
- Cost reduction: HIL cuts the cost of (wet) testing by allowing the validation of systems like subsea control modules and remotely operated vehicles (ROVs) in a controlled environment.
- Increased operational uptime: Systems validated through HIL don’t take equipment away from real-world operations, minimizing downtime for equipment and vessels.
- Improved safety: Critical failure scenarios, such as subsea equipment malfunctions or emergency shut-downs, can be safely rehearsed without endangering personnel or assets.
- Faster deployment: Offshore industries can benefit from reduced prototyping cycles and quicker commissioning of control systems.
- Enhanced product reliability: HIL enables rigorous testing of remote handling equipment, ensuring tools like ROVs, robots, and control systems perform reliably under extreme conditions.
- Risk mitigation: Simulations of hazardous scenarios, such as high-pressure failures or deep-sea environmental challenges, reduce operational risks during field deployment.
- Cost-efficient innovation: Subsea and offshore engineers can test and refine designs for complex systems, like underwater ROVs, without requiring expensive physical prototypes.
- Maintain standards in safety: HIL helps ensure offshore equipment meets stringent safety and environmental standards, reducing the associated risks when deployed in the real world.
- Prototype testing: Incorporating highly realistic physics simulation, the virtual environment is a safe space for prototype testing ahead of real-world production.
How to ensure successful HIL implementation
There are a number of technical barriers that must be overcome when developing and deploying an effective hardware-in-the-loop simulator. One of the key aspects of any simulator setup is the need to avoid latency and create real-time interactions.
Speed can be impacted by different factors, including the hardware running the simulator, the functioning of communication channels, and the level of simulation detail. It can be hard to understand where to draw the line in terms of detail. An important step is to pinpoint what’s essential and what’s a ‘nice-to-have’ in terms of simulated assets interacting with the environment, the level of detail in the related physics simulations, and the selection of sensors and actuators included in the simulation. Tree C has the capacity to implement highly complex physics simulations, like soil interactions or tensioning systems, while safeguarding real-time performance.
Making the business case for a Tree C simulator
When you work with Tree C to develop your simulator, this is a collaborative effort. We help you find and adjust the right level of detail for your needs. It’s good to know that Tree C simulators can develop with your project. New assets, environments, even the complexity of simulated processes can always be added in later stages.
The power and versatility of Tree C’s simulator framework gives your organization the ability to recreate complex real-world environments and use them for a variety of purposes throughout your project or equipment life cycle. That’s important when you consider the initial investment needed to bring it to life and a motivation to start with simulation early in the process, which will ensure maximum return.
Tree C’s flexible simulator framework can be used for multiple purposes, including a HIL setup for offshore, subsea, and remote handling operations. If you’d like to take a deep dive into the possible use cases, we explored them in a previous blog: The Value Of Versatility In Simulators And How To Maximize Your ROI.
A Tree C Simulator is like having real-world working environments and conditions – such as a vessel operating offshore or below water – in a box that you can take anywhere. And by feeding it with real-world data gathered from sensors, it’s even possible to precisely recreate the actual environment where real-world operations take place.
Being able to plug in real software and computational hardware into the simulator framework opens up other opportunities alongside testing and training:
- Equipment and machinery manufacturers can use it to demonstrate real-world hardware, and enable end clients to take it for a test drive in realistic, virtual, environments.
- Offshore and subsea operators can use it to showcase their capabilities in a particular environment using specific equipment, machinery, and vessels in support of winning contracts.
To discover more about flexible simulator solutions from Tree C, get in touch with one of our team. Contact us